What is Lean Six Sigma?
Lean Six Sigma is a process improvement methodology designed to eliminate problems, remove waste and inefficiency, and improve working conditions to provide a better response to customers' needs. It combines the tools, methods and principles of Lean and Six Sigma into one methodology for improving your organisation's operations. There are three key elements:
1. Tools and analytical techniques - that are used to identify and solve problems;
2. Process and methodology - that organise the use of the problem-solving tools to identify root causes and implement solutions
3. Mindset and culture - that relies on data and processes to achieve operation performance goals and continuously improve.
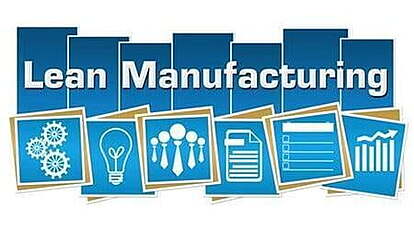
Reduce waste by reorganising a process
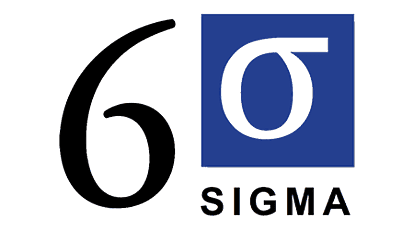
Reduces defects by solving problems
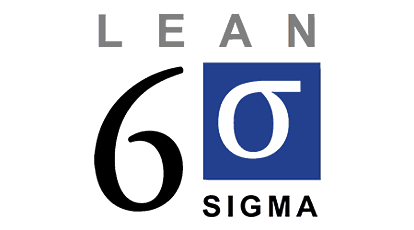
LEAN improves SIX SIGMA: Reducing waste and solving problems to be more efficient and effective
Lean: 8 Wastes

Lean IT 5S tool for Information Systems
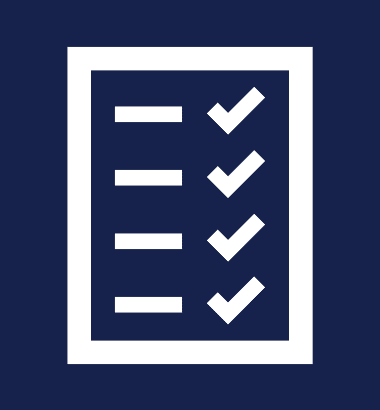
Sort
Use value stream mapping to identify wasteful steps in the information flow, document them and start initiatives to eliminate them.
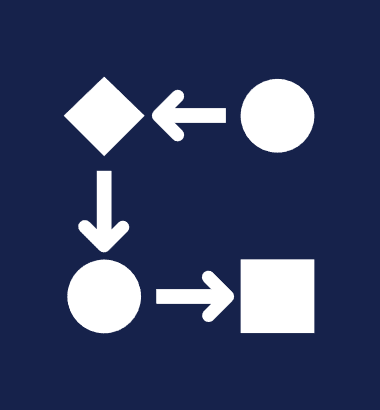
Set in Order
Minimise paperwork. Procedures should be simple and clearly identify the next step, and be intuitive for all users
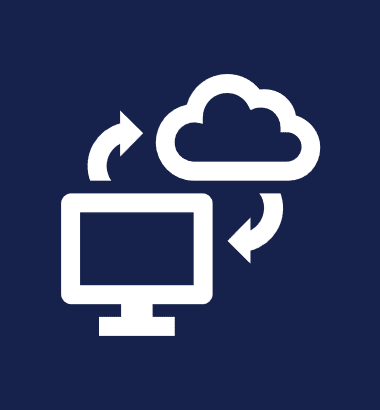
Shine
Clean up data systems and software. Where possible migrate from desktop applications to the cloud for additional security and automatic updates.
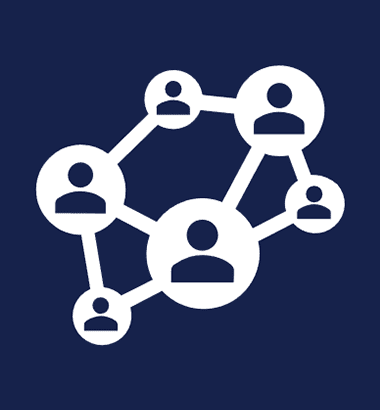
Standardise
Derive standards, patterns and models for best practices that can be applied to other areas. Establish a 'common data environment' for these best practices with change control and governance procedures
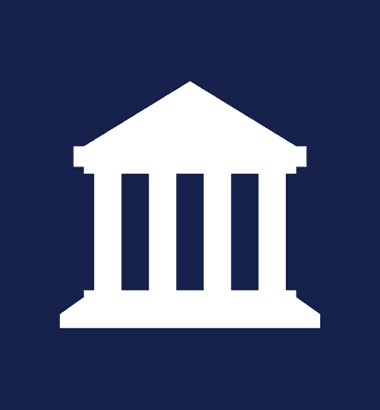
Sustain
Focus on developing a methodology for sustaining the improvements made using the first four steps. Maintain a cycle of continuous improvement process.
Six Sigma DMAIC tool for Change Control
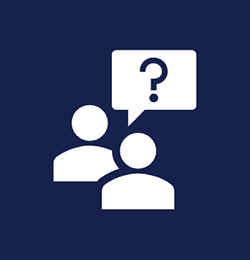
Define
Define the improvement in performance or the replacement of existing processes by a problem statement that defines the object, defect, extent and impact.
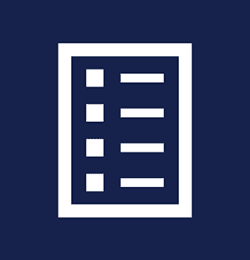
Measure
The change initiator should outline a detailed description of change, the reasons for the change, technical evaluation and a list of impacts based on the data that is available.
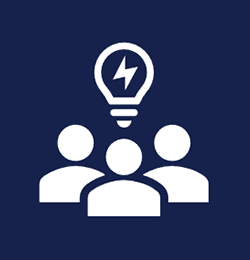
Analyse
The proposed change and any options should be analysed by all stakeholders that will be affected by the proposal including an impact assessment and risk analysis.
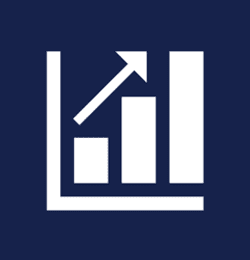
Improve
The change request should be subject to performance qualifications. Statistical evaluation of all affected parameters should be performed against the outputs of the process.
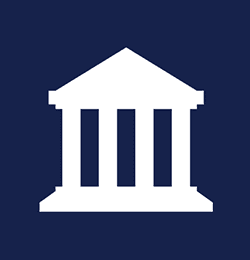
Control
Controlling and maintaining the change is essential to the project's success and newly implemented changes should be assessed at regular intervals to ensure they are running effectively
Infra Hub apps apply the Lean IT - 5s tool to focus on reducing customer's waste. Infra Hub also looks to deliver apps with a focus on continuous improvement by removing the causes of defects (errors) and the variation (inconsistency) in business processes using statistical methods and the DMAIC tool. This is a key method within Six Sigma.